Inspection and Measurement Equipment
Our finished projects go through a rigorous inspection and measurement process. PGI Steel is proud of the quality of our work and the accuracy of the parts we provide. PGI Steel has all micrometers recalibrated per our ISO 9001:2015 certified Quality Management System. Our inspection department maintains the integrity of all measuring & inspection equipment in the machine shop.
Our Measuring Equipment includes, but is not limited to, the following:
- Hexagon 7-Axis Absolute Portable CMM Arm
- Renishaw Probing Systems – Accuracy specified to 0.0005” – .0.001”
- Mitutoyo Profilometers
- Inside / Outside Mics
- Depth Mics
- Vernier Calipers
- Cal–X–Tenders
- Digital Height Gauges
- Dial Bore Gauges
- Threaded Plug Gauges, Metric and Standard
- Small Hole Gauges
- Telescoping Gauges
- Pin Gauge Set
- Precision Jo-Block Set
- Precision 24” Master Square
- Precision Straight Edges
- Master Setting Rings
- Precision Granite Surface Tables
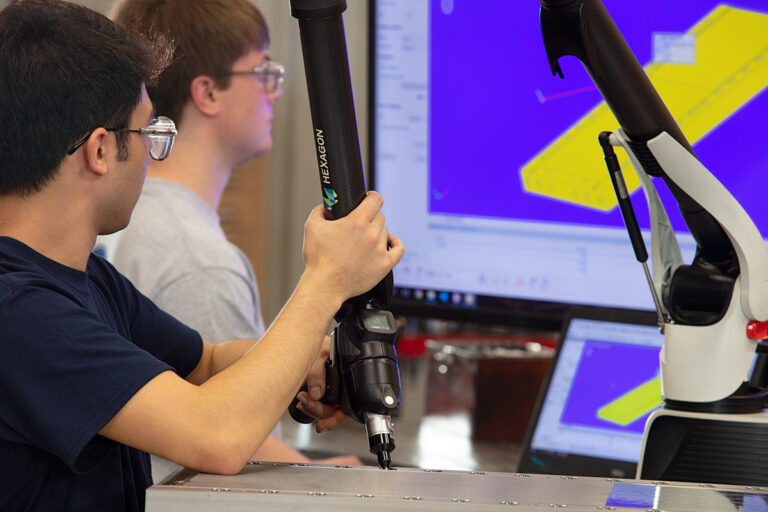
General Tolerances and Measurements
Unit of Measure
- The standard unit of measurement is inches.
- Metric conversions will be made using 1″ = 25.4mm and/or 1mm = .03937″
- The following tolerances are used unless otherwise specified on the customer’s drawing:
Dimensional and Location Tolerances
Decimal Precision | Linear Tolerance | |
.0000″ | = | +/- .0005″ |
.000″ | = | +/- .005″ |
.00″ | = | +/- .010″ |
.0″ | = | +/- .015″ |
Fractional (1/x) | = | +/- 1/32 |
Angular | = | +/- 1 degree |
Machined Finish
Standard machined finish will be .125 RMS
Reamed Holes
Reamed holes will be machined to a Press Fit (PF) of .0005″ to .001″ under specified diameter.
Threaded Holes
- Threaded holes will be chamfered major +1/32″ approximately 90 degrees from machined side
- Full thread depth will be 1.5 x Major diameter
- Minor diameter will be drilled to 65% – 75% thread, depending on material machinability
- Minor diameter will generally be drilled to [(full thread depth) + (tap chamfer length) + .100″] full depth
- Thread fit will be 2B
Counter Bored and Counter Sunk Holes
ANSI standard, as per Machinery Handbook normal fit specifications, will be followed with depth altered to sink application bolt head approximately .015″ below flush
T-Slots
ANSI standard, as per Machinery Handbook normal fit specifications, will be followed.